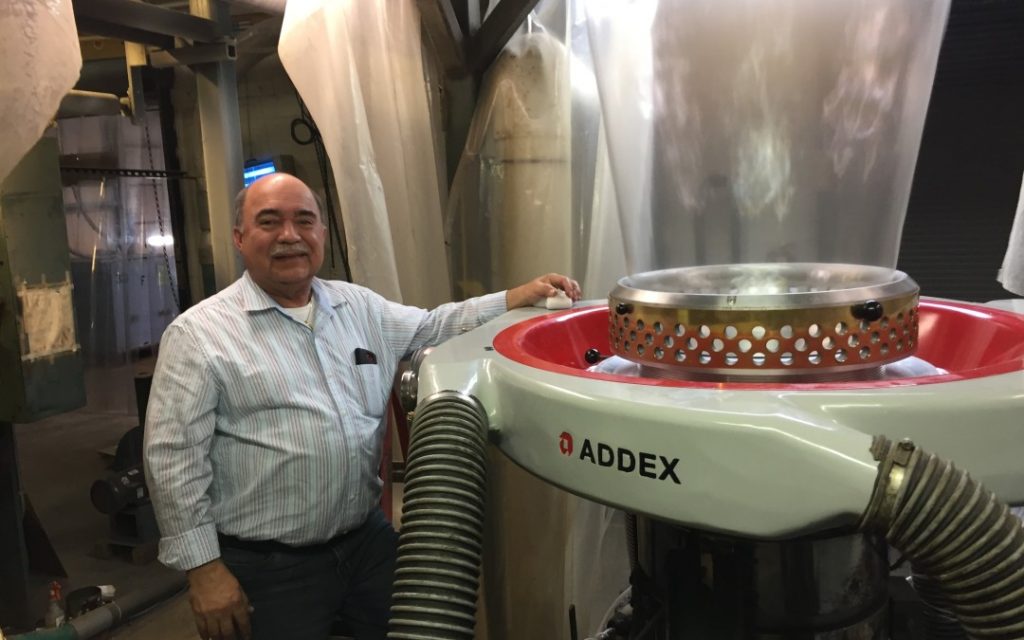
Film processor Dallas Plastics boosts throughput by as much as 40% by retrofitting a new air ring—without the need for IBC.
Output increases equal to that of adding internal bubble cooling without the “expense and headaches” associated with IBC. That’s how Miguel Sanchez described his experience following the installation of a new air ring at Dallas Plastics Corp.’s blown-film plant in Wentzville, Mo.
Sanchez manages that plant, one of three facilities operated by Dallas Plastics, which was established in 1989. The company (dallasplastics.com) specializes in converter-grade films for printing, laminating, and automated packaging, and offers a wide range of specialty films such as narrow-width layflat tubing, critical-tolerance films, non-scratch LDPE, and hightensile-draw tape for drawstring bags. Its films are used in a wide variety of markets that include food, medical, agricultural, retail, automotive, aircraft, and electronics.
Comments are closed