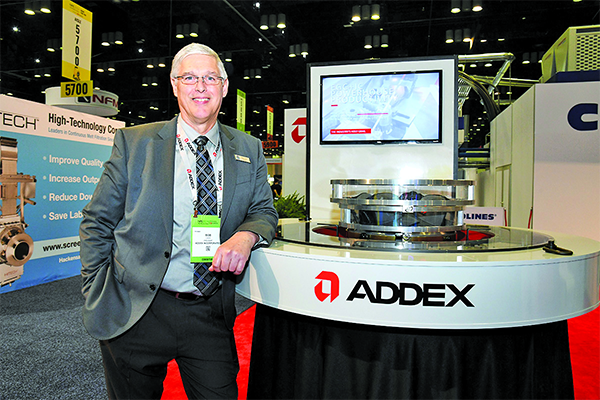
By Beatriz Santos, Sustainable Plastics, May 13, 2024
What do the works of Dutch graphic artist MC Escher and plenum retrofits for existing blown film lines have in common? They make the impossible possible.
That’s just what equipment manufacturer for blown film cooling equipment Addex Inc. has done with its NPE debut.
Historically, single-inlet plenums have featured only one blower hose, which facilitates an easier installation and creates space around the die. However, they have the reputation of being unable to deliver an even-gauge profile. As a result, multi-inlet air rings have typically outperformed single-inlet plenums because they divide air flow into multiple, closely spaced inlets with corresponding improvements in gauge control.
In response to customer demand, Addex has designed a single-inlet plenum with the performance of a multi-inlet plenum. The company’s new patent-pending aerodynamic design employs dual counterflow channels that direct air flow in two opposing directions inside the plenum.
These two counterflows of air join inwardly together to create a combined uniform flow of air to the lip set. The measured overall profile performance is better than with a conventional multi-inlet air ring and inlet effects aren’t seen in the film, which was thought impossible in the industry.
“MC Escher had a type of graphic artwork called regular division of the plane, where figures are perfectly interlocked, there’s no intervening spaces. We actually took that idea and applied it to airflow,” Addex’s President Bob Cree told Sustainable Plastics, a sister publication of Plastics News.
“What we have here is a shape which regularly divides, meaning if you mirror image it, there’s no intervening spaces between it,” he said. “So that when you take the flow from one and you add it circumferentially with the flow from the other, you end up with a combined flow that is perfectly uniform.
“We eliminated the inlet effects by multiplying them by two — by making it twice as bad — but ended up with just the opposite. That’s what’s special about this,” he said.
Addex has tested the new single-inlet plenum against its own multi-inlet plenum, running the two simultaneously. It has found exactly the same profiles.
Other advantages of a single-inlet plenum include a reduction in hoses from eight or more down to a single hose. This saves space on the plant floor, providing easier access around the die for maintenance and operation, and completely eliminates the common problem of multiple hoses having variable lengths and bends leading to negative effects on the finished thickness profile.
Auto-profile for rotating dies
Addex also employs this new single-inlet plenum design in combination with its auto-profile external gauge control (EGC) system, providing an improved starting point before control and better end results. The system was first launched at K 2022, but Addex has been continuously developing it to reveal “shocking” improvements at NPE. The new Gen 3 EGC can be retrofit to existing blown film plastic lines with rotating dies.
The new auto-profile system for rotating dies is based on Addex’s Generation 3 air ring technology, which can reduce gauge variation by more than 50 percent. The system operates much like the one for stationary dies but with added features, including the EGC air ring having a series of “fingers” that open or close to adjust localized air volume. A 12-inch air ring includes 168 control zones with more than 200 control zones on larger systems.
1-degree mapping
This new rotating die-enabled technology is facilitated by a proprietary mapping algorithm embedded within Addex’s latest Gen 3 control technology. The algorithm corrects for die rotation effects in real time.
“The central controller is where all of the thinking is done,” Cree said. “Then we have modules that we can plug into it that do different things.”
On the show floor, the control was set up to do auto-profile for the profiles coming in from the air ring. The critical point for doing auto-profile for rotating dies is the controller’s ability to do 1-degree mapping.
There is much to be gained by having the ability to control such minute details. It results in better profiles, which in turn allow operators to use less film, which lowers both costs and the carbon footprint of the product.
‘Massive’ levels of demand
Addex is seeing a “tremendous level of activity” for its Gen 3 technology, which it is planning to trade secret.
“We are seeing massive demand; it’s shocking me,” Cree said. “I mean we’re getting phone calls out of the blue of people asking whether we can really do this. I would have said it was impossible to do what we’re doing, but the mind-bending suddenly made sense — and we made it.”
Comments are closed